User friendly material support User friendly adjustable depth distance Adjustable and extendable fence profile system Opens reference holes for screwing during milling operation Engine Power: 0,55 kW 230V, 50Hz Bar: - Sizes: 55x50x55 Total Weight: 33 1 pc Hinge milling drill bit 2 drill bits. Milling is done using a cylindrical milling tool mounted in a milling tool holder that is then mounted in the tool spindle on the machine. End Mills End mills are the most common milling cutters. End mills are available in a wide variety of lengths, diameters, and types. A square end mill is used for most general milling applications.
Joinery and industrial woodworking machinery:
CNC milling machine, Hinge boring machine, 6 axis
TEKNO X2
Milling - anuba hinge inserting machine with 6 interpolated axis, TEKNO X2 is suitable for an industrial production of doors and frames.
It is adrdress to manufacturers of doors with anuba system and hinges system.
Anuba inserting and drilling head and milling head management by numerical control.
Woodworking
The TEKNO X2 machine is suitable for the woodwork of doors and frames for Italy and the countries that adopt the anuba and hinge systems.
After a simple programming of the job to be performed, the machine will (through the loading and unloading belts) load the door to be processed and then start the milling, boring and anuba screwing processes previously set.
The milling and anuba head is automatically positioned according to the values introduced in the program, reducing the time of mechanical setting of the machine.
Detailed woodworking
- hole keyholes
- drilling for handle
- milling for lock
- drilling and anuba screwing
- drilling double anuba
- milling for hinge
- milling for concealed hinge
Advantages

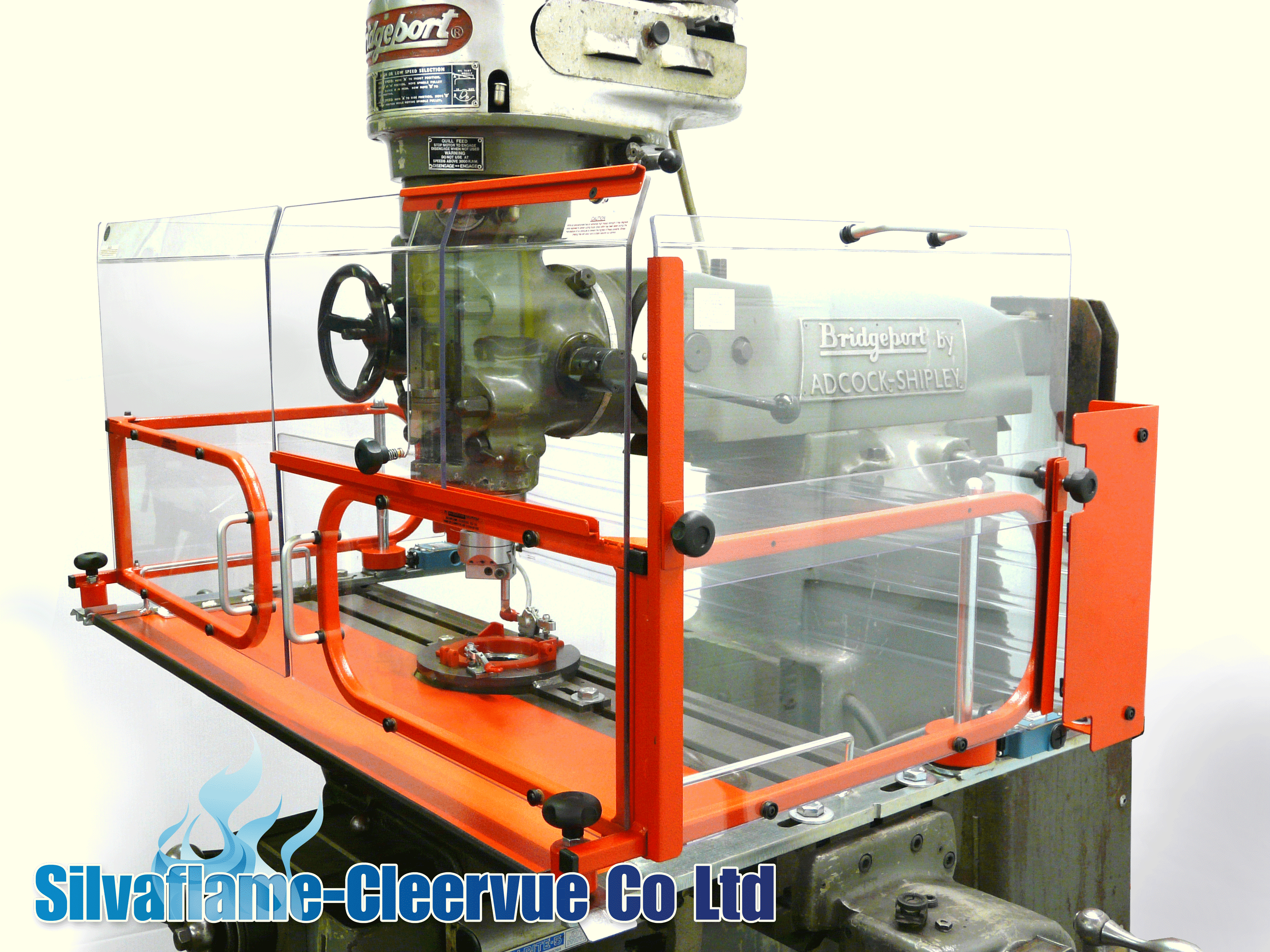
- The machine TEKNO X2 can be configured either as working cells or as throughfeed machines, thanks to its structure and loading and unloading belts.
- The machine performs a complete production process of milling, boring and anuba screwing on a door, in about 2 minutes and with a single positioning, allowing the operator to fit and fix its unmounted hardware.
- Complete with 15' color touch screen.
- The software includes macro presets that allow a quick parameter setting.
- Remote technical support ensured by the parent company in direct interaction with our specialists to help customers with the settings or changes of the parameters.
- The machine is completely Made in Italy, with internal manufacturing of the body, its columns and some of the parts through the internal welding department equipped with CNC metalworking machines.
Technical features

Hinges working area from RH and LH stops | 2500 mm |
Min. door width | 550 mm |
Max. door width | 1250 mm |
X axis stroke | 600 mm |
X2 axis stroke | 2650 mm |
Y axis stroke | 930 mm |
Z axis stroke | 300 mm |
Electro-spindles for lock machining | no. 1 |
Electro-spindle for drillins and millings | no. 1 |
Gear motor for anuba hinges screwings dia. 13/14mm | no. 1 |
Inclination of anuba hinges fitting device | -3° +10° |
Gear motor power for anuba hinges screwing | 0,75 HP - 0,55 kW |
Motors power lock side | 1,5 HP - 1,1 kW |
X-X2-Y-Z motors power axis | 2,4 N/m |
P motor power axis | 1,2 N/m |
Automatic positioning of milling-anuba inserting head | standard |
Colour touch screen | 15' |
Automatic loading/unloading belts | standard |
Motorized stretcher to simplify the door lodging | standard |
Automatic centralized lubrication of axis | standard |
No. 1 cutter dia. 16 | standard |
No. 1 cutter dia. 14 | standard |
No. 1 drill dia. 7 | standard |
Dimensions | 2600 x 3400 x 1750 mm |
Weight | 1200 Kg |
Optional features
- Kit for frame machining
- Loading/unloading roller conveyor
Container load dimensions
- 2300 x 3200 x 1765 mm
- August 22, 2019
Milling is a common machining process that involves the use of a machine, known as a milling machine, to remove material from a stationary workpiece using a rotating cutting tool. With milling, the workpiece remains stationary, whereas the cutting tool rotates. As the rotating cutting tool presses against the workpiece, it removes material.
While all milling machines follow this same basic formula, there are different types of milling machines, each of which has its own unique characteristics. In this post, we’re going to explore the differences between horizontal milling machines and vertical milling machines.
What Is a Vertical Milling Machine?
The most common type of milling machine, a vertical milling machine features a vertically oriented spindle that holds, as well as rotates, the cutting tool against the stationary workpiece. The spindle is capable of moving up and down — all while pressing against the workpiece to remove material.
There are actually two distinct types of vertical milling machines: turret milling machines and bed milling machines. In a turret milling machine, the spindle and table can move perpendicular and parallel to the axis. In comparison, bed milling machines only move the table perpendicular to the axis. Many manufacturing companies prefer turret milling machines because of their versatility. They are able to perform a wider range of milling operations than bed milling machines, making them a smart investment for manufacturing companies.
Steel T Slot Milling Table
What Is a Horizontal Milling Machine?
Slot Milling Cnc
Horizontal milling machines feature a similar design in which a spindle containing a rotating cutting tool presses against a workpiece to remove material from the workpiece. With that said, horizontal milling machines differ from their vertical counterparts in several ways. The biggest difference between these two types of milling machines is the orientation of the spindle. With vertical milling machines, the spindle features a vertical orientation. With horizontal milling machines, the spindle features a horizontal orientation. In other words, horizontal milling machines mount the cutting tool on a horizontally oriented spindle that’s able to selectively remove material from the stationary workpiece.
Furthermore, horizontal milling machines usually feature different cutting tools than vertical milling machines. While vertical milling machines usually have long and thin cutting tools, horizontal milling machines have shorter and thicker cutting tools.
Horizontal milling machines are able to perform heavier, deeper cuts than vertical milling machines. As a result, manufacturing companies often use them to cut grooves or slots into workpieces. Hopefully, this gives you a better understanding of the differences between vertical milling machines and horizontal milling machines.